From heavy machinery to hazardous chemicals, factories and industries can be dangerous places if you don’t take proper precautions. As the employer, it’s on you to ensure the safety of your employees at work. But how to do that? What should be a priority? How to properly manage these risks? With such questions in mind, our specialists crafted this article, aiming at giving you an overview of Health & Safety in the manufacturing industry, outlining the main hazards, necessary PPE, and key considerations for different sectors.
This article is the first of three in the Essentials series, covering manufacturing, construction, and vulnerable workers, so stay tuned to explore our specialists’ take on these important Health & Safety issues!
Health & Safety in manufacturing
Health & Safety in the manufacturing industry are all about minimizing the risk of workplace incidents and illnesses. You need a proactive approach to identifying potential hazards, implementing control measures, and providing employees with the knowledge and tools they need to work safely. This means going beyond simply hanging up a poster or two and making a dedicated effort to create a culture of safety. Think regular training sessions, clearly communicated safety procedures, and open communication channels for reporting concerns.
Hazards in manufacturing
Manufacturing environments present a wide range of hazards, and understanding them is the first step towards effective manufacturing Health & Safety. Here’s a breakdown of some common ones.
Manual handling
Tasks involving lifting, carrying, pushing, or pulling heavy objects can lead to musculoskeletal injuries (MSIs). Think strains, sprains, and back problems. Proper training on lifting techniques, using mechanical aids when possible, and implementing ergonomic workstations are crucial for preventing these injuries.
Noise
Loud machinery and processes can cause irreversible hearing damage. Regular noise level monitoring, providing hearing protection like earplugs or muffs, and creating designated quiet zones can help protect workers’ hearing.
Dust
Many manufacturing processes generate dust, which can cause respiratory problems like asthma and lung disease. Effective ventilation systems, dust extraction equipment, and respiratory protective equipment (RPE) like masks are essential for controlling dust exposure.
Electricity
Faulty wiring, damaged equipment, and improper use of electrical tools can lead to electric shocks and fires. Regular inspections of electrical systems, proper procedures for maintenance, and ensuring workers are trained to identify and avoid electrical hazards are vital.
Vehicles
Forklifts, trucks, and other vehicles operating at a manufacturing facility pose a risk of collisions and pedestrian injuries. Clearly marked traffic routes, designated pedestrian walkways, and comprehensive training for vehicle operators are crucial for preventing accidents.
Slips, trips, and falls
Slippery surfaces, cluttered walkways, and uneven flooring can cause slips, trips, and falls. Good housekeeping practices, including keeping work areas clean and organized, and implementing anti-slip flooring in high-risk areas can significantly reduce these incidents.
Working at heights
Tasks that require working at heights, such as on platforms or ladders, carry the risk of falls. Providing appropriate fall protection equipment like harnesses and guardrails, and ensuring workers are trained in safe working at height procedures, is essential.
Chemicals
Many manufacturing processes involve the use of hazardous chemicals, which can cause skin irritation, respiratory problems, or even more serious health issues. Proper labelling and storage of chemicals, providing appropriate personal protective equipment (PPE) like gloves and respirators, and ensuring workers are trained in safe handling procedures are vital. This is where WHMIS training comes in. Remember, employers are responsible for providing WHMIS training to their employees, ensuring they understand the hazards associated with the chemicals they work with and how to handle them safely.
Using heavy machinery
Operating heavy machinery like presses, cutters, and robots can lead to severe injuries if not handled correctly. Training on machine operation, implementing machine guarding to prevent accidental contact with moving parts, and enforcing strict lockout/tagout procedures for maintenance are crucial for safety.
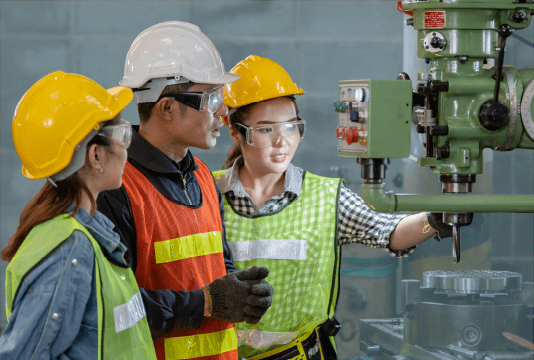
The correct PPE for a factory worker
Personal protective equipment (PPE) is the last line of defence that protects workers from hazards. The type of PPE required depends on the tasks employees are doing and the hazards associated with them, but here are some common safety items:
- Safety footwear: Steel-toe boots or shoes to protect feet from falling objects or crushing hazards.
- Eye protection: Safety glasses or goggles to protect eyes from flying debris, chemicals, or intense light.
- Hearing protection: Earplugs or muffs to protect against noise-induced hearing loss.
- Respiratory protection: Masks or respirators to protect against dust, fumes, or other airborne contaminants.
- Hand protection: Gloves to protect hands from cuts, abrasions, chemicals, or extreme temperatures.
- Head protection: Hard hats to protect against head injuries from falling objects or impacts.
- High-visibility clothing: To ensure workers are visible in low-light conditions or around moving vehicles.
Industries
Different manufacturing industries have unique Health & Safety considerations:
- Plastic: Workers may be exposed to hazardous chemicals and fumes during plastic processing. Proper ventilation, PPE, and training on safe handling procedures are essential.
- Glass: The risk of cuts and lacerations from broken glass is high. Appropriate PPE, including cut-resistant gloves and safety footwear, is crucial.
- Paper: Dust and noise are major concerns in paper manufacturing. Controlling dust levels through ventilation and providing hearing protection are important.
- Food: Hygiene and sanitation are paramount in food manufacturing to prevent contamination. Workers must be trained in proper food handling practices and wear appropriate PPE, such as hairnets and gloves.
By understanding the specific hazards and implementing appropriate control measures, you can create a safe and healthy working environment for all employees. A strong commitment to Health & Safety in the manufacturing industry both protects workers and contributes to increased productivity and a positive workplace culture.
Health & Safety training for factory workers
Effective training is the cornerstone of Health & Safety in the manufacturing industry. Training empowers workers to identify hazards, understand safe work practices, and respond appropriately in emergencies. But what does effective training actually look like? It’s not just a one-time event, but an ongoing process that adapts to the evolving needs of the workplace.
Here are some key aspects of comprehensive Health & Safety training for factory workers:
- Orientation and onboarding: New employees should receive thorough training on general safety protocols, emergency procedures, and the specific hazards they may encounter in their roles.
- Job-specific training: This covers safe operation of machinery, proper handling of materials, and any specialized safety procedures relevant to their tasks.
- WHMIS training: As we discussed earlier, this is crucial for workers who handle hazardous chemicals. It ensures they understand labels, safety data sheets (SDSs), and safe handling procedures.
- Lockout/tagout procedures: Training on these procedures is essential for preventing accidents during machinery maintenance or repair.
- Emergency response: Workers should be trained on how to respond to various emergencies, such as fires, chemical spills, or medical incidents. This includes knowing evacuation routes, using fire extinguishers, and providing first aid.
- Refresher training: Regular refresher training reinforces safe work practices, introduces updates to safety protocols, and addresses any new hazards that may have emerged.
Remember, training should be engaging and interactive. Consider incorporating hands-on exercises, real-life scenarios, and visual aids to enhance learning and retention.
The consequences of poor Health & Safety
The consequences of neglecting Health & Safety in manufacturing can be severe, affecting individuals and businesses. Let’s take a closer look at the potential repercussions:
- Workplace injuries and illnesses: These can range from minor cuts and bruises to life-altering injuries or fatalities. The effect on workers and their families can be devastating, both physically and emotionally.
- Increased costs: Workplace incidents lead to direct costs like medical expenses, workers’ compensation claims, and lost productivity. Other costs can include damage to equipment, investigation time, and potential legal fees.
- Damage to reputation: A poor safety record can tarnish a company’s reputation, making it difficult to attract and retain skilled workers. It can also lead to loss of business and damage to customer relationships.
- Legal penalties: Noncompliance with Health & Safety regulations can result in hefty fines and even legal action.
- Decreased morale and productivity: A workplace where safety is not prioritized can lead to low morale, increased stress, and reduced productivity. Workers who feel unsafe are less likely to be engaged and productive.
Get Health & Safety support for manufacturing
Need a hand with Health & Safety in your manufacturing business? Citation Canada is here to help. We have the right tools to set your business up for success, such as Health & Safety software, content, and support. These solutions bring together advanced technology and unrivalled professional expertise, providing you with services like Health & Safety documentation, risk assessments, or even live advice.
Don’t wait for an accident to happen! Book a free demo at a time that fits your schedule and our experts will provide a free, no-obligation quote tailored to your needs in as little as one business day. Also, check out our FREE toolkit—your go-to resource for everything on workplace Health & Safety!